Our Blogs
Fleet Management()
Car Rental Software()
Fleet Drivers()
Infographics(0)
News(0)
Service We Offer
Follow Us
How to Manage Fleet Downtime with Fleet Management
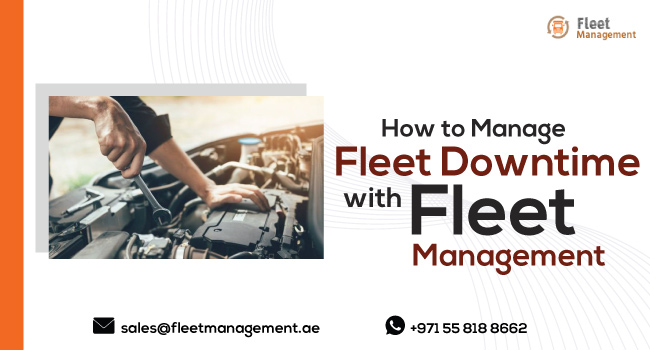
One of the major worries of fleet managers is Fleet downtime. The period when a vehicle is not available for use is defined as vehicle downtime. The reasons for downtime can be vehicle repair, service, or an accident. Weather conditions and traffic congestions may cause the vehicle to be stranded and out of the road.
Sometimes, you may have to pull a vehicle out of the road because of driver issues. Conditions like weather, accident and traffic cannot be controlled. But we can proactively plan to minimize downtime loss caused due to these reasons.
Preventive maintenance and service can help reduce downtime caused due to vehicle conditions. In this blog, we will discuss the costs incurred due to fleet downtime and how an effective fleet management system can help deal with downtime.
Costs Incurred Due to Fleet Downtime
On average, the costs of fleet downtime can be anywhere between Rs 2000 and Rs 20,000 per day depending on the type of business. If you have a car rental business, then the cost of vehicle downtime will be even higher as you will not get your day’s or week’s rental income. The other costs that you may incur because of vehicle downtime are:
- Cost to rent a replacement vehicle
- Loss of revenue because of missed appointments
- Salary of the driver of the unused vehicle
- Late penalties
- Cost of replacement parts
- Extra payment for premium services and repairs
- If transporting goods, extra manpower to transfer goods from damaged vehicle to replacement vehicles
- Delay in deliveries
How you can Minimise Downtime with a Fleet Management Software?
Fleet management software offers a convenient solution to manage the entire fleet and even automate repetitive tasks. The software can be customised based on your business model and requirements.

This application can also help identify possible causes of fleet downtime to address them in the early stages itself. Let’s explore the different ways in which fleet management software can help minimise downtime and improve fleet productivity.
Preventive Maintenance Program
Regular service is very important to maintain good vehicle health. The fleet management software keeps track of the maintenance checks of each vehicle in your fleet. It also sends notifications to remind you of the regular maintenance and services.
Read Also: Importance of Predictive Analysis in Fleet Management
The system can also be configured to send notifications once the vehicle has travelled 3000 to 5000 kilometres. The fleet manager can check the distanced travelled on the dashboard or check the notifications and send the vehicle for service.
Address Serious Vehicle Issues Immediately
There’s an old proverb that says, “An ounce of prevention is worth a pound of cure.” A lot of money and time can be saved if minor repairs are tackled immediately.
If small issues are not immediately checked, they can cumulate to become a huge problem, which can keep the vehicle off the road for days. You can use the software to create a form that allows the driver to submit details that the driver feels are not “ok” with the vehicle.
For example, wheel alignment needs to be done or that the brakes need to be checked. The fleet manager should take these forms seriously and address the issues immediately. Checking and repairing these small issues will just need a few hours. If left unchecked, they could lead to an accident or long downtime.
Replace Fleet Vehicles after a few years/set number of kilometers
To get the best productivity from your fleet, you need to maintain the vehicles in prime condition. If the vehicle has travelled a few lakh kilometers, then it is time to “retire” the vehicle and bring in a new vehicle.

It is because as vehicles get old, they may not be able to meet the strenuous demands of your business. And may need service and maintenance more often. The software will have details of when you purchased the vehicle and the number of FCs that was done. It will help you evaluate the age and performance of the vehicles in your fleet.
Check Replacement Parts
When you’re getting replacement parts for the vehicles, it is vital to check if they are genuine. You will be paying good money for the spare parts, so make sure they are of quality. Poor quality spare parts not only drain your money but can also lead to vehicle problems in the future.
You can monitor the replacement parts using the software tool. It will help you maintain details of the spare parts you purchased, which vehicle they were used for and when it was purchased.
All this information will help you monitor the expenses involved in replacement parts. It will also give you an estimated date when the oil, tires, brake shoe, and other parts need to be replaced.
Use the Right Vehicle for the Job
To ensure optimum fleet productivity, you need the right vehicle for the job. When you do your basic research while building the fleet, consider vehicle lifetime, maintenance, gross vehicle weight (GVW) and payload that is required for the job.
Also, the vehicle you choose should depend on the terrain, location and purpose. If you’re getting a vehicle for school or college trips, then it should fairly have a good amount of seating as well as safety features.
Read Also: 31 Ways to Reduce Fleet Maintenance Costs
On the other hand, class and comfort will be the top priority when you’re looking to add vehicles to your luxury car rental service. With the right kind of vehicles, you can get more out of your fleet.
Track Driver Behaviour
One of the reasons for vehicle downtime is driver behaviour. If the driver is prone to rash driving and is inconsistent at work, your vehicle may be off-road more than on road.
The fleet management software helps you monitor driver behaviour based on various criteria like drive time, vehicle repairs, number of accidents, and reports from others. If a driver is not regular to work, then you may have to pull the vehicle out till you arrange for a replacement vehicle or driver.
It can cause an additional burden and cost on your fleet management. Using the software, track driver behaviour. You can reward good and consistent drivers and remove drivers who are causing more vehicle downtime.
Data Analytics to Track Fleet Productivity
The fleet management system maintains all fleet data, from the number of kilometers travelled and route to number of services and replacements. The fleet manager can analyse all the data to find the vehicles /drivers that are most productive and those that are the least.

Data analysis can help find the reason for vehicle downtime and also to build an effective fleet management strategy.
Make Staff Accountable
Motivate drivers to be accountable for their vehicles. It would also help if you have a reward system that will encourage the drivers to take good care of their vehicles and minimise downtime. When the drivers are satisfied with their work environment, they are more likely to perform better.
This in turn will help improve your fleet productivity. You can set up a dashboard that lists drivers who made on-time deliveries or drove one whole month without even one accident. These little gestures can help boost morale and prevent downtime because of driver issues.
Proper Pre and Post Trip Vehicle Inspections
It is important to maintain Daily Vehicle Inspection Reports and route vehicle inspection reports. The fleet manager or a mechanic can do a complete check-up of the vehicle before and after a long haul.
This inspection can help identify services and repairs needed. If you have a fleet where the vehicles travel within the city but round the clock, then schedule weekly inspections. Update all the information in the database for reference and further action.
Read Also: What is fleet management – All you need to know
The fleet manager can do a periodical evaluation of all the inspections to check if all the vehicles are in proper working condition.
Surprise Field Inspections
Apart from regular inspections, services, and maintenances, it also helps to do surprise field inspections. It will help catch any unexpected problems or reasons for downtime right in the early stages itself.
Conclusion
It is not possible to completely stop vehicle downtime. But with proper planning and effective use of a fleet management system, you can reduce the expenses and issues caused due to fleet downtime.
The software lets you effectively manage your fleet and improve fleet productivity. Whether you offer corporate transportation solutions or have a cab rental service, our fleet management system can help increase vehicle uptime. Contact us for more details.